GSD Comparison
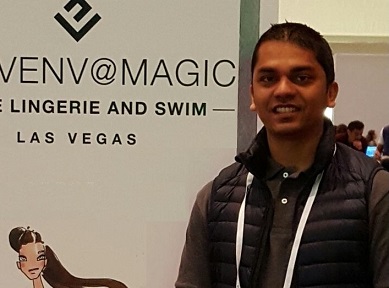
This is adapted from a guest contribution appearing at www.onlineclothingstudy.com/2016/05/lean-management-program-and-pmts-system.html. Charm Rammandala a Lean Management Expert, has shared his Walmart/ASDA experience with apparel lean management programs using PMTS across South Asia. At George Sourcing the apparel sourcing arm of ASDA, UK which is a subsidiary of Wal-Mart, Charm was in-charge of the LEAN management program for Apparel and Home Textiles in George across South Asia.
Our lean project was designed to align suppliers to future pricing challenges the George brand might face. As you know, manufacturing cost is ever increasing yet the price that buyers are willing to pay is same or constantly decreasing. This decrease is due to the competition in high street, where the buyers are not in a position to pay more and risk erosion of their market share. I could buy a formal shirt with a tie for $6 in Wal-Mart and a printed round neck T shirt for $5 at GAP. We all wonder how they do it, as we can’t buy a shirt of the same quality for such low price in our own manufacturing countries.
We have noticed that most apparel and Home Textiles manufacturers suffer due to lack of understanding the work flow and bottlenecks during the final volatile and time sensitive stages of the process. As a result they need to increase the factory gate price to sustain the business. Some are now beginning to learn that companies like Wal-Mart, Nike and Adidas do focus on helping manufactures to get their act together. This is what LEAN management program does.
SewEasy-GSD is a tool we took on board after some extensive research; we waited till Capturing the Gains white paper was out. As you would agree what we need is a tool that can be implemented to get tangible results. It’s not about presentations, graphs or seminars. We needed a system where associates could be trained in relatively short periods of time, easy to implement and not complicated to benchmark the products by calculating the SAM or SMV as you would call it. Process bench-marking could follow this stage. Obviously cost also is a deciding factor. As you know in the apparel industry, employee turnover is high and every time a new analyst joins in, we need him trained and ready to give the efficiencies the previous analyst gave. Otherwise it’s a waste.
We found Coats-GSD (General Sewing Data, UK) to be a great tool but it was a challenge for floor level associates to handle, took a long time to train and the costs were astronomical. SewEasy-GSD has only few steps, easy to understand and ready to go the moment you buy.
We found a real difference in the efficiency and the productivity after installing SewEasy-GSD in our corporate office and linking it with our supplier partners. More importantly friction between the sewing machine operator (SMO) and the work-study analyst was greatly subsided and in fact it sort of became a partnership, simply because the SMO knew exactly what the time study analysis does and how it helps SMO to earn higher pay through production incentives.
Hope my experience and above comments help you in Lean Management of apparel manufacturing.
Mr. Charm Rammandala, Lean Management Expert